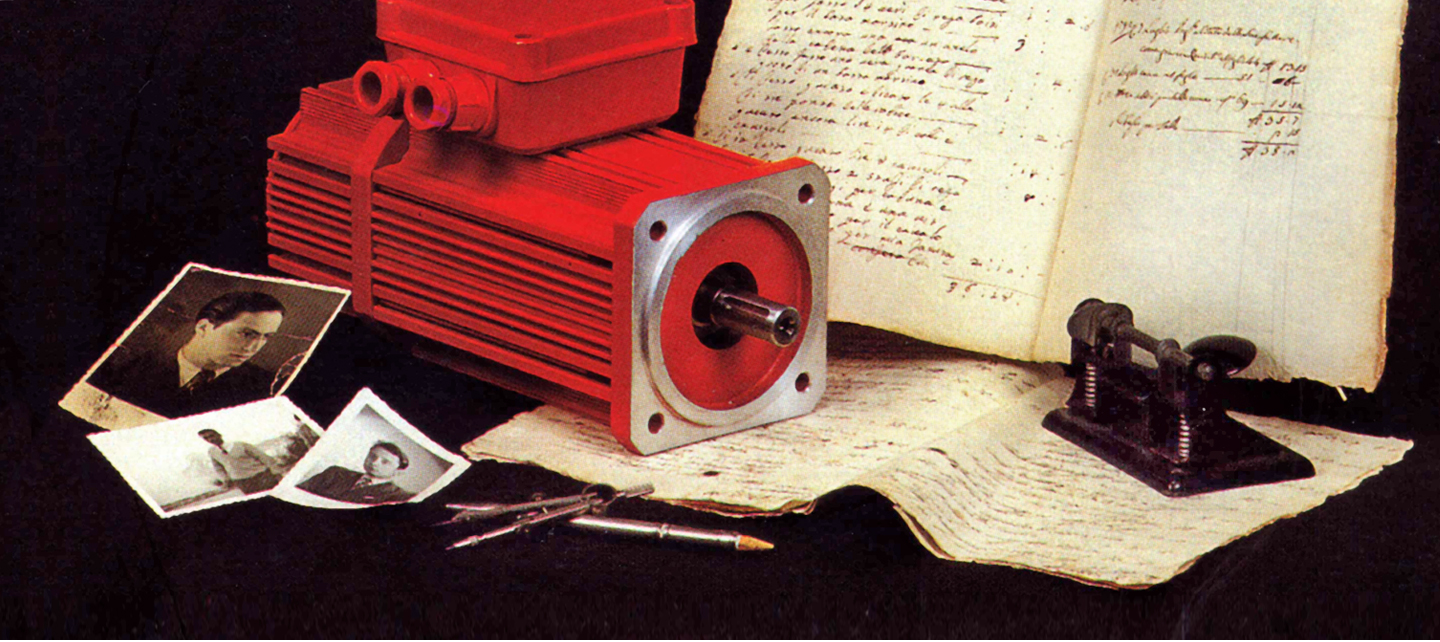
It is thanks to our fathers if we are here today.
From them we inherited resourcefulness and vision.
1958
The story begins
The Comer business project starts: Vittorio Pacinotti, Camillo Lagomarsini and Ferdinando Volpato together begin an adventure that will stay with them for life. The new company is involved in designing and manufacturing transformers and small AC motors
1969
Premises and productivity double
Comer moves into a new building owned by the company, doubles the surface area of the plant and increases production capacity.
1972
First DC motor line
Comer Impianti
The launch of the first line of DC motors entirely designed by Comer alone. This line is soon received by the market and Comer breaks into the complex industry of quality DC motors. Alberto Baroni and Mario Scarazzato kick off the Comer Impianti sales agency and contribute to the success of Comer around the country.
1983
DC motor development
The innovative line of DC motors develops with a rectangular laminated casing for 2-pole motors and a squared casing for 4-pole motors: the smallest is the 2-pole RTL 80 series, the largest is the 4-pole TL 200. They improve the performance of motors in DC and their power/weight ratio.
1990
Special asynchronous vector motors
The first line of asynchronous special "vector" motors appears; it uses the same sophisticated technology as the DC motor materials, applied to an AC motor design.
1995
Quality certification
New extension
Comer puts a quality control system in place and is among the first Italian companies to obtain the ISO9000 certification from the QCS institute. New offices and a new warehouse: with its 4000 sq m. of indoor space, Comer grows in size and capacity to satisfy even the most demanding customers.
2000
Motors Powertech Program
Powertech Program, the new line of special asynchronous motors with fully laminated casing is launched: high performance, compact size, attractive design; the Fluid AX series is developed with a liquid cooling circuit. The uniqueness of these engines draws the attention of important industrial groups who choose COMER as their partner.
2006
Comer Solutions
Comer Impianti becomes Comer Solutions, the new sales agency owned by Comer.
2009
Energy recovery testing room
The innovative testing room with 2.5MW obtained completely through energy recovery is inaugurated: respect for the environment and cutting edge technology to offer maximum technical support to customers.
2010
Torque permanent magnet motors
The first set of Torque permanent magnet motors is unveiled. These boast high polarity and an extremely high torque/size ratio. From the same basic design comes the series of generators in the 30kW-200kW range, to be installed on small wind turbines.
2011
Photovoltaic systems and the safeguarding of the environment
The 140kW photovoltaic system is created to satisfy 75% of the domestic energy needs of the company and to avoid the emission of about 90 tonnes of CO2 each year. Comer's ecological awareness for the protection of the environment is renewed.
2014
Wind generators
Vacuum impregnation systems and drying ovens
The first 100kW wind turbine is created with high performance 50rpm "direct drive" and a 710mm shaft height. A new expansion: the modern vacuum impregnation machinery and the new curing furnace system are manufactured; in addition the use of the latest formulated resins with a low environmental impact means that Comer ensures a further increase in product quality.
2015
The largest motor
This is the year that the largest motor is designed and built by Comer: 710mm axis height, 80,000Nm maximum torque, 1.7MW maximum power at 200rpm, the first of a series which goes up to 150,000Nm.
2016
Into the future
The journey towards the future continues. New functional and innovative applications are designed, futuristic materials are tested out. The corporate communications plan is developed: there's a new logo while web site content and style is updated to describe the company values and commitment of its people.
What's our dream? It's to leave the indelible mark of our passion on our daily work.
2017
Second collaboration with Edinburgh Design
Similar application to the previous one but bigger: more than fifty Comer synchronous motors, uncooled, shaft height 200 mm., are submerged into the water with the same previous function of a Flowave Pool
2019
Technical development of motors Ip68 | Ul/CSA Certification
Going deeper into IP68 technology: synchronous small motors, uncooled, shaft height 132 mm.
In February 2019 Comer gets a Certification of Compliance UL/CSA for the most required motor sizes in North-American market.
2020
Motor for energy stocking application
The Company manufactures the longest motor ever made before, specifically dedicated to a revolutionary energy stocking system: 2 m. long induction motor, shaft height 315, lowest-loss lamination.
2021
Submerged stainless steel motors | Innodriver 2019
The experience is consolidated on submerged motors: this time the motors, in addition to the previous features, have been completely made of stainless steel. A great production challenge!
As our participation to Innodriver 2019 tender, it has been developed a comparative study on synchronous motors having innovative rotor design (variable reluctance) with/without rare-earth magnets.